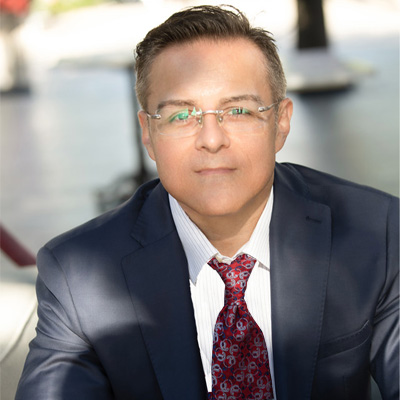
Example of how to calculate net free area:
1200 square foot attic divided by 150 square feet = 8 square feet (1200 / 150 = 8)
8 square feet times 144 square inches = 1152 square inches (8 x 144 = 1152)
1152 square inches divided by 2 = 576 square inches at soffit and at exhaust (1152 / 2 = 576)
Head: Round metal piece at the top of the nail
Shank: The length of the nail between the bottom of head and the point. May be smooth or have rings, flutes or spirals for greater holding power.
Point: Sharpened end opposite the head for greater ease in driving.
Gauge: Reference how thick a nail is, with lower number indicating greater thickness.
Length: Distance from the bottom of the head to the sharp point of the nail.
Rigidity: The bending and shear resistance of the nail.
Brite: No coating to protect the nail from corrosion if exposed to high humidity or water, not recommended for exterior use or treated lumber, and only for interior applications where no corrosion protection is needed, i.e. interior trim, framing, and finish.
Heat-Treated: Heated to extreme temperatures and then cooled quickly; this produces very hard steel that can be used with hardened materials such as concrete and masonry. This is still vulnerable to corrosion, and should be used in interior applications.
Phosphate Coated Nails: Reduces friction during installation and increases corrosion protection. Produced by dipping in a solution of zinc or manganese acid phosphate; it has a dark grey finish that provides a surface that binds well with paint and joint compounds with minimal corrosion resistance. Most commonly found on drywall fasteners, not recommended for exterior and treated lumber.
Vinyl Coated Nails: A slick vinyl coating helps ease driving of the fastener—when the fastener is driven, it’s briefly heated by the friction and quickly cools down, hardening the vinyl coating; offers some extra holding power but does not protect the fastener from corrosion; recommended for interior applications where no corrosion protection is needed.
Electro Galvanized Roofing Nails: Zinc plating process in which a layer of zinc is bonded to steel to protect against corrosion; smooth, shiny finish, which is generally used in areas where minimal corrosion protection is needed.
Galvanized Nails: Coated with a protective layer of zinc for corrosion resistance and weather exposure.
Hot Dipped Galvanized Roofing Nails: Most common method of galvanization where iron, steel or aluminum are coated with a thin zinc layer, by passing the metal through a molten bath of zinc that results in very high corrosion resistance suitable for some acidic and treated lumber; will corrode over time as the coating wears, but generally good for the lifetime of the application; typically used in outdoor applications—meets ASTM A153.
Stainless Steel Roofing Nails: Used where both the properties of steel and corrosion resistance are required; although stainless steel does not readily corrode, it isn’t fully stain proof—certain conditions can and do affect it such as low oxygen, high salinity, or poor circulation environments; 300 series stainless makes up 70% of all stainless used, and is the most corrosion resistant, ductile, and weldable type of stainless steel; these alloys are subject to crevice corrosion and pitting corrosion.
304 / 305 grade stainless steel alloys are the most versatile and widely used of stainless steel contains 18% chromium and 8% nickel; recommended for exterior applications where a higher level of corrosion resistance is desired.316 (also called marine grade) has superior corrosion resistance versus other chromium-nickel steels when exposed to chemical corrodents such as sea water; slightly more nickel and the addition of 2% molybdenum is what makes 316 considerably more resistant to corrosion than the 304 family; recommended for marine environments.
What Does a Penny Mean?
The "d" when referring to nail sizes, stands for penny. When the Romans occupied what is now England, they had a coin called the denarius, which was also the name for an English penny, so the "d" is an abbreviation for denarius. The "d" indicates the nail's length. The larger the number, the longer the nail. For example, a 3d is smaller than a 10d. When nails were hand-forged, penny sizes referred to the price for 100 nails. The longer the nail, the higher the cost. The system was used in England into the 15th century, but is now obsolete. However, the penny size is still included along with the length on retail boxes of nails today.
2d | 1 inch | 25 mm
3d | 1-1/4 inches | 32 mm
4d | 1-1/2 inches | 38 mm
5d | 1-3/4 inches | 44 mm
6d | 2 inches | 51 mm
7d | 2-1/4 inches | 57 mm
8d | 2-1/2 inches | 65 mm
9d | 2-3/4 inches | 70 mm
10d | 3 inches | 76 mm
12d | 3-1/4 inches | 83 mm
16d | 3-1/2 inches | 89 mm
20d | 4 inches | 102 mm
30d | 4-1/2 inches | 115 mm
40d | 5 inches | 127 mm
50d | 5-1/2 inches | 140 mm
60d | 6 inches | 152 mm
0 | 0.0365 inch | 7.785 mm
1 | 0.2830 inch | 7.188 mm
2 | 0.2625 inch | 6.667 mm
3 | 0.2437 inch | 6.189 mm
4 | 0.2253 inch | 5.722 mm
5 | 0.2070 inch | 5.257 mm
6 | 0.1920 inch | 4.876 mm
7 | 0.1770 inch | 4.495 mm
8 | 0.1620 inch | 4.114 mm
9 | 0.1483 inch | 3.766 mm
10 | 0.1350 inch | 3.429 mm
11 | 0.1205 inch | 3.060 mm
12 | 0.1055 inch | 2.679 mm
13 | 0.0915 inch | 2.324 mm
14 | 0.0800 inch | 2.032 mm
15 | 0.0720 inch | 1.828 mm
16 | 0.0625 inch | 1.587 mm
17 | 0.0540 inch | 1.371 mm
18 | 0.0475 inch | 1.206 mm
19 | 0.0410 inch | 1.041 mm
20 | 0.0328 inch | 0.883
Finding The Proper Degree
To determine the proper fastener length and degree, place your strip of nails on the chart below. Position the shank of the first nail over the grey line, with the nail point over the black dot in the lower left corner.
Roofing nails are used for applying roofing asphalt shingles, insulation board, and felt to wood substrates. The large head and heavier shank gauge provide greater holding power. Roofing nails come in a variety of styles to fit multiple job requirements.